Over the years TDA has developed optimal processes to distribute its goods. Not only do we start sorting out items during teardown, but we also have a large amount of stock available in our warehouses across the globe. This allows us to act fast and deliver quick, no matter what the demand is.
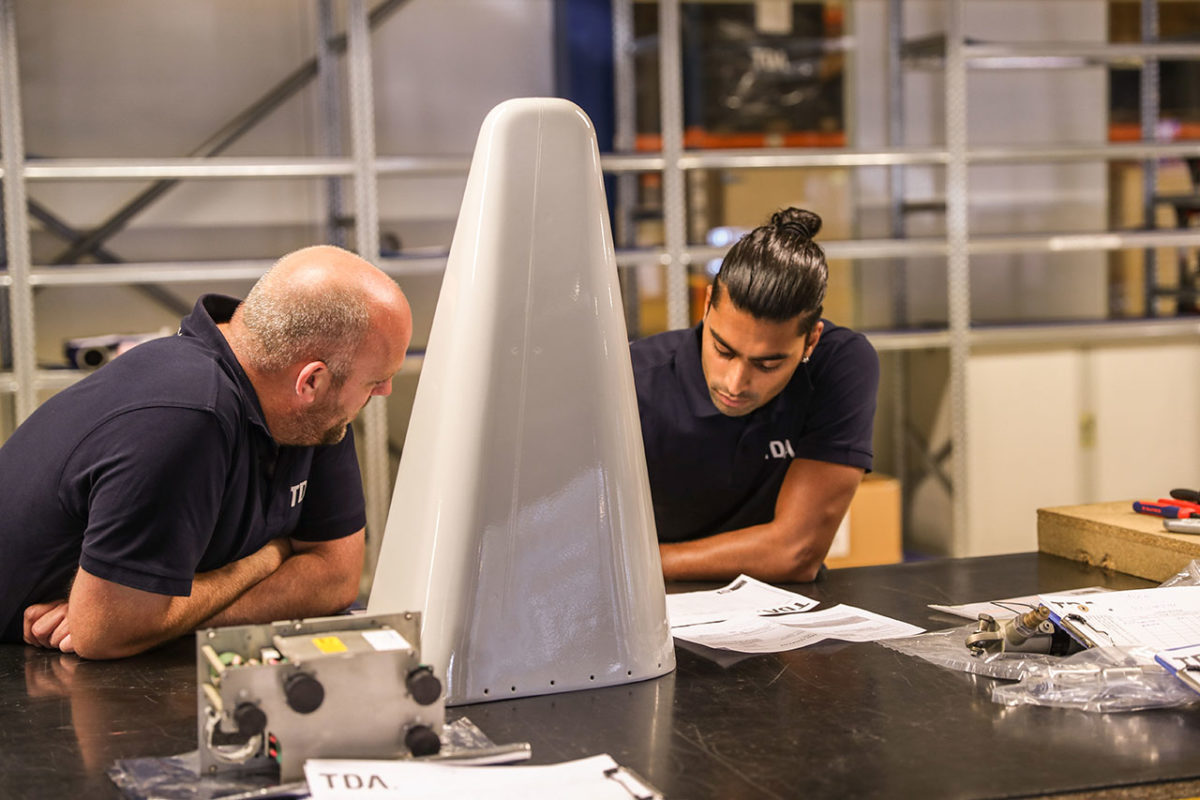
Starting at teardown
During the disassembly of an aircraft, (group of) parts are sorted out for distribution. We follow a very efficient process where during the teardown we already select special order items and offer these to interested parties. This could include interior items for MRO shops and cockpit cuts for simulation companies.
Besides this, we ship the majority of high value and hot items to numerous reputable repair shops as soon as possible. This allows for a quick turnaround in overhauled or serviceable condition, which means we have multiple quantities of the items tagged, stored and ready to go. This way, we create a pool of narrow-body parts which are primarily used for exchange purposes with end-users.
Since the selection starts at teardown, this is a very time-efficient process. A large part of the harvest at this point is already on its way to becoming serviceable and overhauled or are being removed by specialists for their new owner.
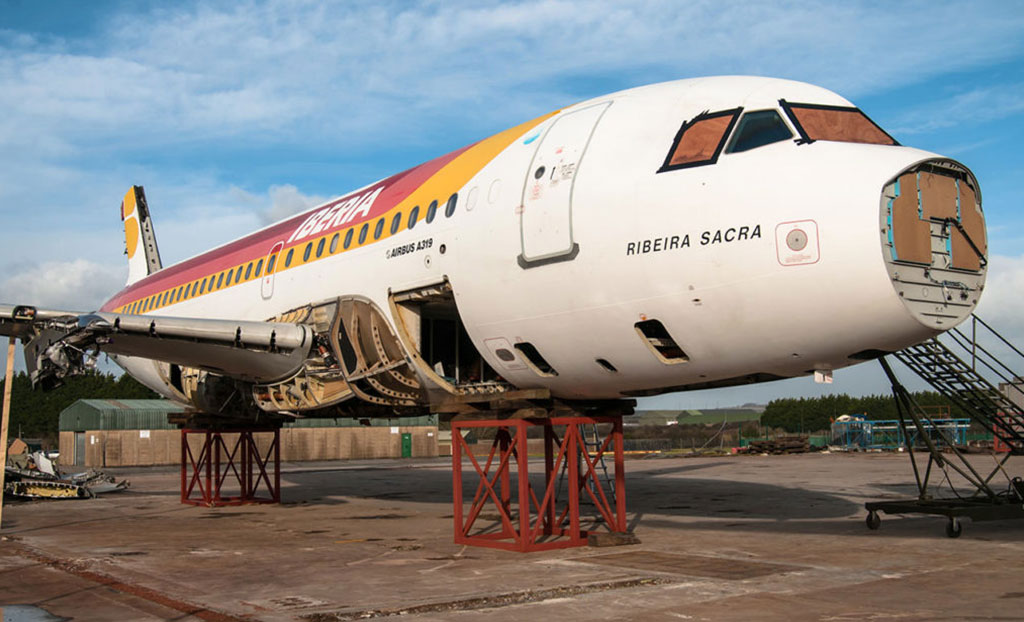
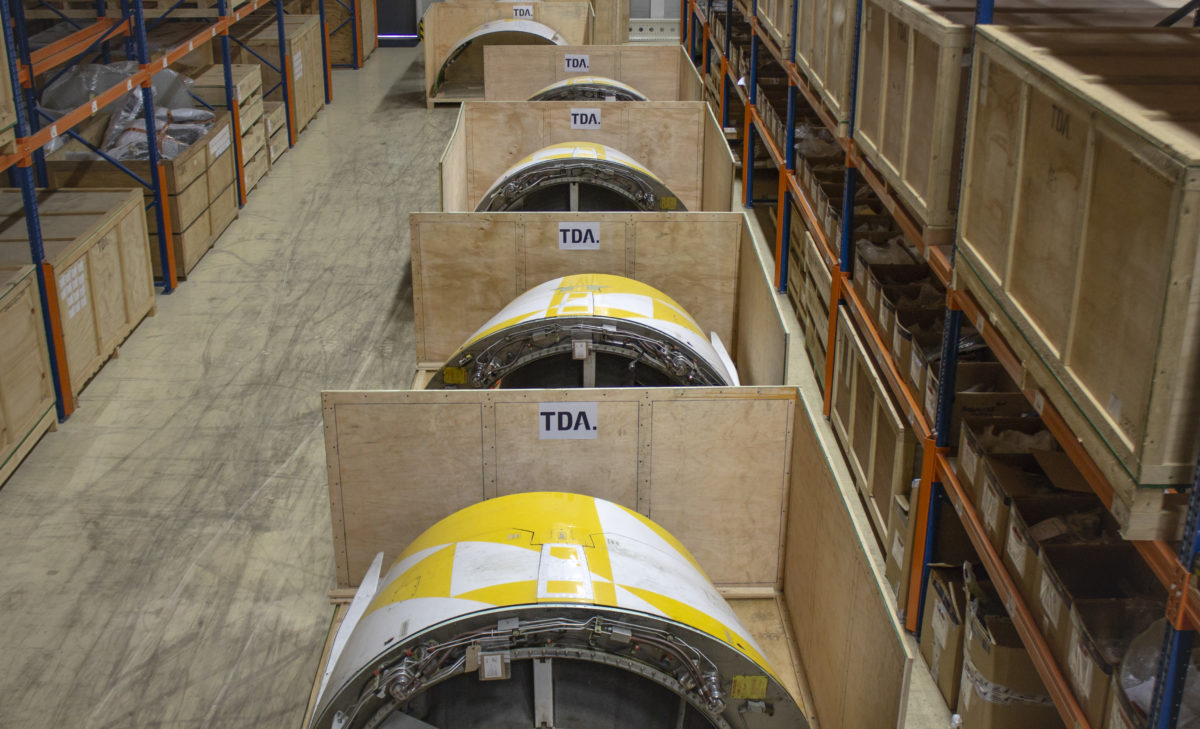
Stored and selected
We try to distribute the stock to our warehouses in a strategic way by looking at the demand in the USA, UK and European market. For the high demand, high value or hard-to-get items, we monitor the number of stocked items and relocate the items depending on each warehouse’s stock. This means we always have the right parts available in the right place, at the right time.
Our efficient processes allow us to service our clients fast, across the world. The part you’re looking for is only 24 hours away!